System solutions in best quality
As a full-service partner, we accompany our customers from the initial technological idea to the end of production, thus offering real added value.
Certifications Automotive Standard - Optical 3D metrology - SPC - Laboratory - Complaints management - Problem-solving methods - CT analyses - Grinding surface joint analyses weld seams
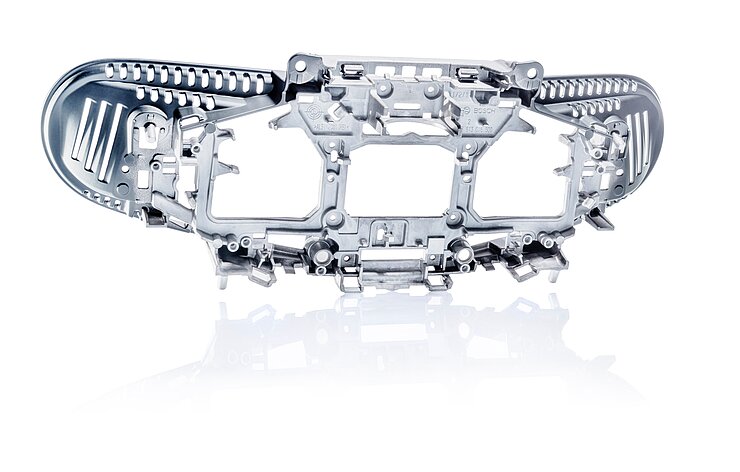
Process technology Aluminum die-casting
Alupress produces aluminum die cast components of the highest precision and quality. In-house simulations before the start of the project, sophisticated tool design and in-house tool production, combined with minimum quantity spraying in the casting process, bring measurable added value for our customers.
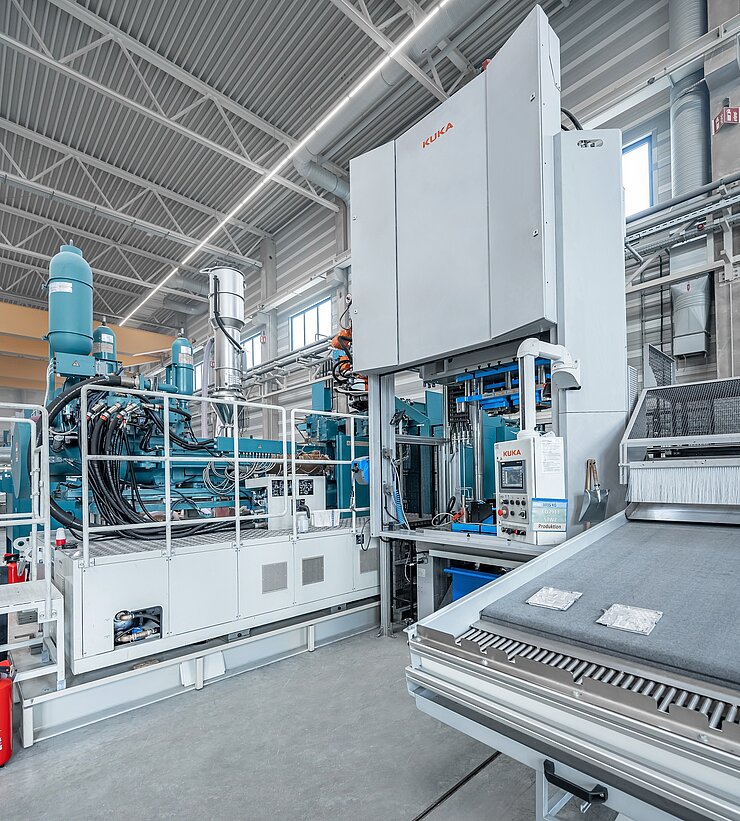
Process technology Magnesium thixomolding
The magnesium thixomolding process makes it possible to produce components even more precisely and with thinner walls than with conventional magnesium die casting.
Magnesium parts are approx. 33% lighter than aluminum parts of the same volume. For components, where weight plays a role, but plastic cannot be used (e.g. on account of thermal conductivity), magnesium is a suitable alternative.
Laser beam welding and cooling solutions
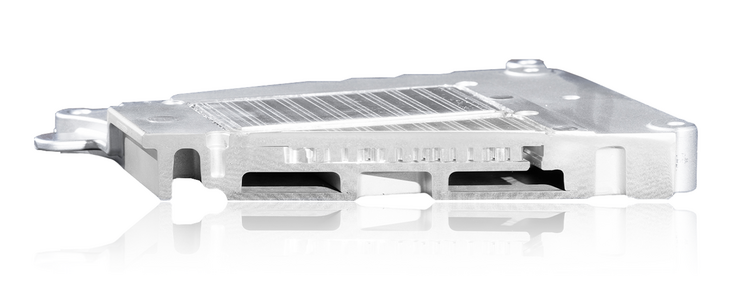
Cooling solutions
Our cooling solutions optimize the thermal performance of products. We laser-weld various components to die-cast aluminum that have been manufactured by extrusion, impact extrusion, sintering or 3D printing of aluminum alloys with superior thermal conductivity.
Advantages of our cooling solutions
Our Cooling solutions offer the following advantages:
- Up to 30% improved thermal resistance at the contact point to electronics
- Up to 60% improved thermal conductivity in the area of cooling benches through laser welding of conductive inserts
- Reduction of CO2 footprint by up to 70% compared to conventional cooling solutions through the use of secondary alloys
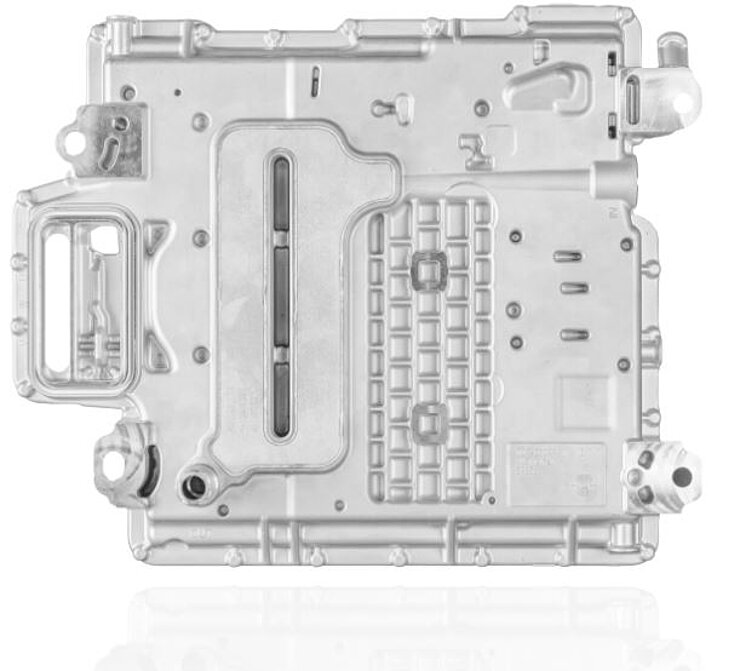
Laser welding
Our components for e-mobility are laser welded in order to meet our customers' requirements in terms of weight reduction, cost efficiency and improved thermal performance.
Advantages of laser welding
In terms of a comprehensive increase in performance, we offer the following advantages with the laser welding process:
- Reduction of welding cycle time by a factor of 5 to 10 compared to standard solutions
- Lightweight design and reduction of component dimensions in the order of 30% through the use of laser beam welding
- Cost-efficient, scalable production
- Possibility of laser welding conductive inserts
Advantages of laser welding
The following advantages are available with the laser welding process, offering all-round increased performance:
- Reduction of welding cycle time by a factor of 5 to 10 compared to standard solutions
- Potential for lightweight design with weight reduction in the order of 30% through the use of laser beam welding
- Cost-efficient, scalable production
- Possibility of welding conductive inserts
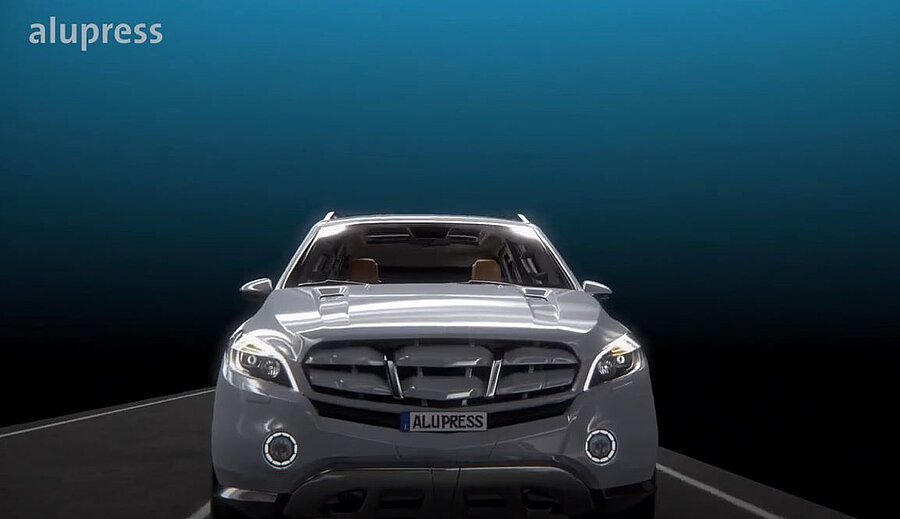